【食品加工業様へ】 製造実行システム導入
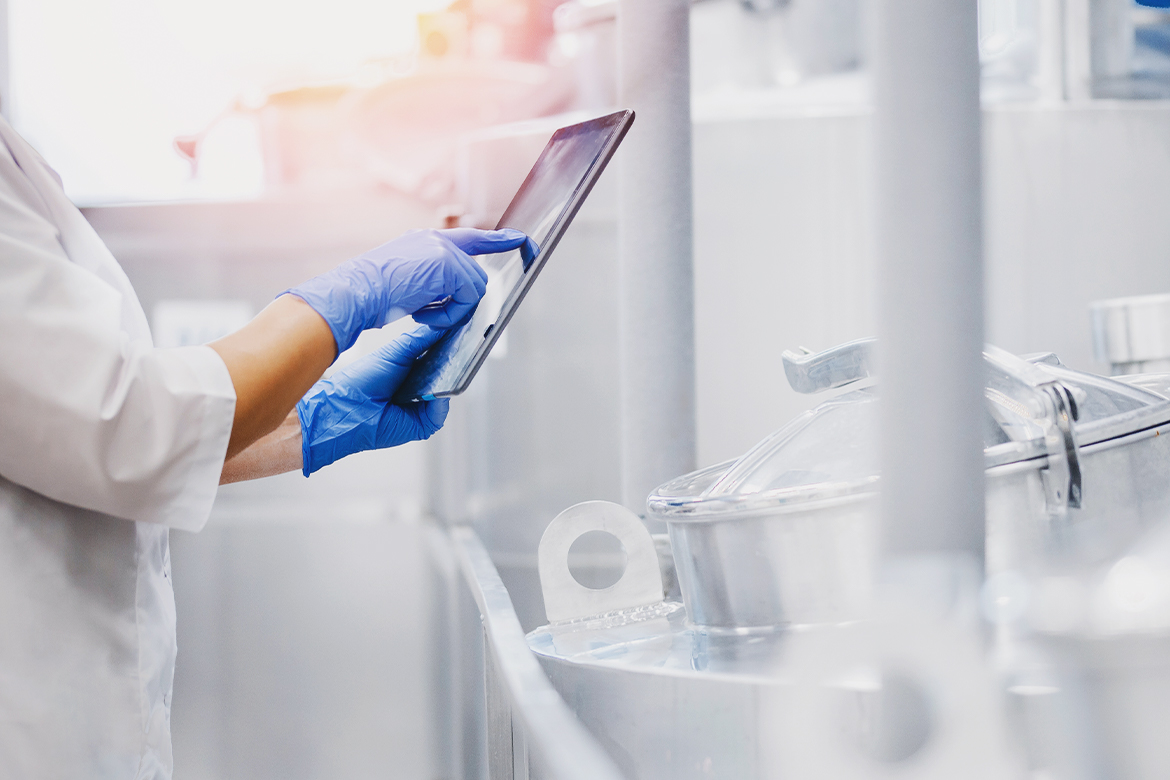
生産ラインの作業状況や在庫の情報把握、部署間のリアルタイム連携により
製造コスト削減とトレーサビリティを確立。
PROBLEMお客様の課題
- 現場担当者の経験と勘に依存し、属人化・非効率・高コストになっている。
- モノづくりの状況が「見えず」、評価・改善活動のサイクル化が難しい。
- 問題が発生しても、生産・加工および流通など製品の移動をトレースできない。
その他、各製造工程別の課題
- 受入/入庫(ロットトレース管理)
製品の原料・包材ロットの特定とその出荷先が分からない - 指示/払出(払出指示書)
誰が、いつ、どのタイミングで、どのロット原料の在庫を確保したか分からない - 製造(製造指示書・レシピ)
誰が、いつ、どのタイミングで、どのロット原料(使用)・製造ロット(製品数)を製造したか分からない - 検査(検査指示書・調書)
誰が、いつ、どのタイミングで、どの製造ロット(全件・抜出)を検査したか分からない - 在庫移動(移動指示書)
誰が、いつ、どのタイミングで、どの製造ロットを製品庫から出荷置き場へ移動したか分からない - 出荷(出荷ピッキング指示書・荷札ラベル・出荷伝票)
誰が、いつ、どのタイミングで、どの製造ロットをどこへ出荷したか分からない
SOLUTIONインフォファームによる提案と解決
製造実行システム(MES)を導入によりトレーサビリティを確立。生産ラインの作業状況や在庫情報の把握、各部署間のリアルタイム連携で、製造コストの削減にも成功しました。
その他、以下のような連携・管理を可能にしました。
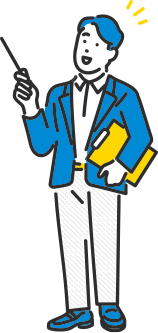
POINT01
製造部門との連携・機械・設備のマスタ情報を管理し、制御や稼働監視を可能に
・工場内の無駄を省き、リソースの最適化と稼働率を向上
POINT02
サプライチェーンとの連携・各部署間の情報連携により、的確な生産スケジューリングと需要を予測
・リアルタイムのコミュニケーションにより、在庫変更による手配も容易に
POINT03
製品のフィードバック情報の管理・製品ロットやシリアル番号とあわせて、品質やトラブルのフィードバック情報を管理
・トラブル時の追跡や、不良品発生防止に効果を発揮
製造実行システム(MES)導入による製造業務の全体最適化例
モノの管理 | 生産資源の配分と監視 生産装置・工具・技能・資材・その他設備や文書など |
---|---|
仕様・文書管理 作業に必要となるドキュメント管理(作業指示書・レシピ(配合表)・図面・作業手順書・設計変更など) |
|
設備の保守・保全管理 装置や工具の可用性確保に、定期保全・予防保全のスケジュール管理 |
|
製品品質管理・履歴管理 収集した測定データによるリアルタイム分析、適正な品質管理、トレーサビリティ |
|
ヒトの管理 | 作業のスケジューリング 生産計画にもとづく詳細なスケジュール立案、勤務シフト対応 |
作業手配・製造指示 生産投入の管理、ジョブ工程・受注オーダ・ロットなどの作業開始終了、時間 仕掛品の場所と次の作業を把握 |
|
作業者管理 作業時間・生産数の歩留管理、作業者状況の監視、最適な作業割り当て |